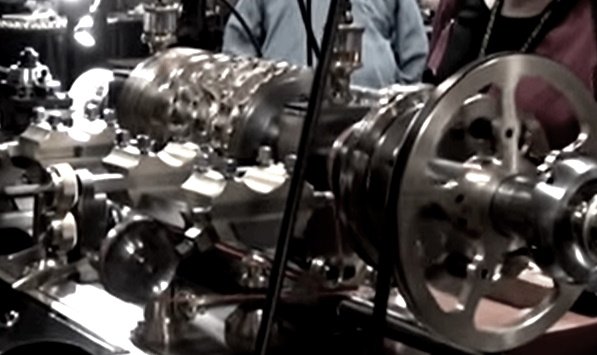
Here’s an old article discussing the Sharpening and Polishing of Cutting Tools used in Ornamental Woodturning:
Although the modern trend in Ornamental Turning appears to favor fairly plain work with little ornamental cutting limited to fairly simple vertical and horizontal fluting capable of being executed with the simplest of form cutters, there are still workers who do like on occasion to use at least some of the very full range of cutters and drills available in the outfits of Holtzapffel apparatus.
I fully realize that many of these tools, particularly the drills, are rather fantastic and cannot properly be applied to present day work.
However, I like to make use of quite a number of these cutters although I have long passed the time when I wanted to cover the entire surface of the work with tiny dust-collecting excavations.
For certain work the diamond is the only practicable tool but for the non-Geometric-Chuckers and the impoverished who require more than round-nosed and angular cutters, the carbon steel tool is still the only one to use.
To obtain a satisfactory polished edge on all types of cutter quickly something better than the Goneostat-cum-oilstone etc. is demanded. ‘
The most enthusiastic is apt to get weary of repeated and laborious stoning.
I therefore decided to make up a compact apparatus containing all the movements required for easy renewal of cutting edges.
I did consider a machine for mechanically applying to tool at the correct angles etc. , but decided it would be exceedingly complicated by the many and varied contours involved.
The plan and side view drawings which follow show, about half size, this collection of appliances which, in use, have proved to be quick and reasonably efficient.
As can be seen it consists of several rotary and one reciprocating oilstones driven from a common shaft which in turn is driven from a small low speed motor.
The shaft, a length of 4’t diameter silver steel, revolves in self-aligning ball races housed in cast aluminium brackets.
The 311 diameter Arkansas oil stone wheel is used for square, angular and round-nosed tools held in one of the several goneostats standing upon the brass table which is adjustable for height.
Interchangeable with the Arkansas stone are India oil stones and cast iron laps.
They are so arranged that they project at different levels above the platform so that, having roughly stoned the edge on the India wheel this is changed for the
Arkansas wheel which is a little lower and therefore polishes a small area on the edge of the tool without the Goneostat setting being altered.
These stones are held by a single screw and it is the work of a moment to exchange one for the other.
These wheels and also the conical oil stones are located in the spindles, also running in ball races in the tubular upright bearing housings.
The conical oil stones, both India and Arkansas, need no comment being used for the concave cutting edges of tools and drills, the tool being presented to the stone at the required angle by hand.
The stones are secured in brass holders by shellac.
The remaining rotary appliance is a spindle running in ball races and having a small split type of chuck.
In this is held to be to arrive at a happy medium of a substance for the disc that will charge with oil stone powder and at the same time will retain a sharp edge so necessary to keeping sharp corners in the little cutters.
The reciprocating holder consists of a square and/or triangular oil stone cemented into brass holders and given an up and down motion by means of a crank and connecting rod, as in the I.C. engine.
The stones are quickly interchangeable, being held in the guides by a single screw.
This type of stone is used for edges of moulded contour drills and for some of the acute angled and often very small cutters used in the various cutting frames.
It is, in effect, a filing machine, the file moving up and down and the tool presented to it at the required angle.
In order to preserve sharp edges and flat surfaces on these stones they can be rapidly dressed on a copper lap charged with fine diamond powder; somewhere around 150 mesh will cut quickly and fairly smoothly.
The small and very short belt drives to these appliances from the back shaft was something of a problem.
The best solution seems to be to use ordinary elastic bands of suitable length.
They are cheap enough and can be slipped on and off quickly.
A large magnifying glass on a universally jointed stand is arranged on the. baseboard (not shown in the drawing).
This is not an unqualified success and for sharpening the small and intricate tools the watchmaker’s eyeglass is much better.