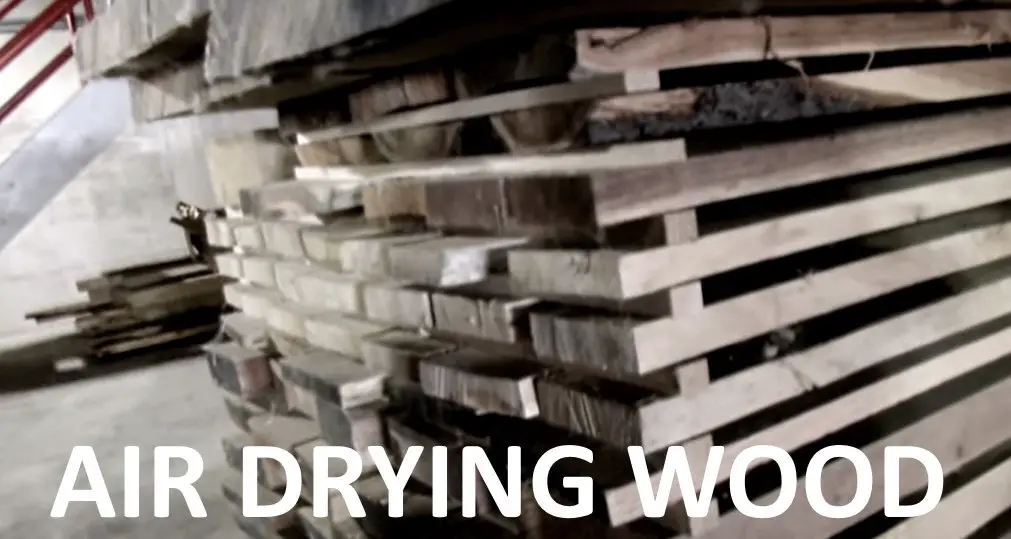
Although many methods of drying timber have been tried over the years only a few of these enable drying to be carried out at a reasonable cost and with minimal damage to the timber.
The most common method of drying is to extract moisture in the form of water vapor.
To do this, heat must be supplied to the wood to provide the latent heat of vaporization.
There are several ways of conveying heat to the wood and removing the evaporated moisture.
Nearly all the world’s timber is, in fact, dried in air.
This can be carried out at ordinary atmospheric temperatures (air drying), or in a kiln at controlled temperatures raised artificially above atmospheric temperature but not usually above 100°C, the boiling point of water.
Air drying and kiln drying are fundamentally the same process because, with both, air is the medium which conveys heat to the wood and carries away the evaporated moisture.
The factors which will be described are those which affect wood when dried in air (in the open or in a kiln).
There are several other ways in which wood can be dried, in chemicals, in a vacuum etc.
Under these conditions different factors come into play.
1. Vapor Pressure and Relative Humidity
To understand how wood dries in air it is necessary to introduce some terminology.
When air holds the maximum possible amount of vapor, the vapor exerts what is called the saturation vapor pressure.
If the water vapor present is less than this maximum then the air can take up more moisture.
The ratio of actual vapor pressure to the saturation vapor pressure at any given temperature, expressed as a percentage, is called the relative humidity (rh).
When a piece of wet wood is exposed to air which is not already saturated (i.e. its relative humidity is less than 100%), evaporation takes place from its surface.
At a given temperature the rate of evaporation is dependent on the vapor pressure difference between the air close to the wood and that of the more mobile air above this zone.
2. Temperature
The temperature of a piece of wood and of the air surrounding it will also affect the rate of water evaporation from the wood surface.
With kiln drying, warm or hot air is passed over the timber and at the start of the drying process the temperature differential between the air and the wet wood will usually be large.
As a result, heat energy will be transferred from the air to the wood surface where it will raise the temperature of both the wood and the water it contains.
Water, in the form of vapor, will then be lost from the wood surfaces, provided the surrounding air is not already saturated with moisture. This results in the development of a moisture content gradient from the inside to the outside of the wood.
As the temperature is raised this increases not only the steepness of this moisture gradient, but also the rate of moisture movement along the gradient and the rate of loss of water vapor from the surface of the wood.
To illustrate the effect of temperature on drying rate, a piece of wood with a moisture content of 16% at the surface and 40% at the core will generally have moisture gradients at 50°C and 80°C which are respectively four and eight times greater than that at 20° C.
With kiln drying, higher temperatures also increase the capacity of the air for moisture.
An advantage of this is that less air needs to be heated and exhausted from the kiln.
In addition higher temperatures allow more rapid conditioning of a timber load to a uniform final moisture content.
Unfortunately the considerable benefits obtainable by raising the drying temperature cannot always be fully exploited because there are limits to the drying rates which various wood species will tolerate without degrade.
In the drying of many species, especially medium density and heavy hardwoods, shrinkage and accompanying distortion may increase as the temperature is raised.
So with species which are prone to distort it is normal to use comparatively low kiln temperatures.
A few species are liable to collapse and/or honeycomb if dried at high temperatures.
Many tend to darken appreciably and, in resinous timbers, drying at temperatures above about 50° C causes the resin to exude on to the wood surface, although this may not necessarily be detrimental for all products or uses.
Finally, since high temperature drying may cause a slight loss in impact strength, it is not advisable to exceed about 60° C when drying timber for items such as tool handles and sports goods.
3. Air Movement
If the air surrounding a piece of wet wood is stagnant and of small volume, it will soon become saturated and evaporation of moisture from the wood will stop.
Even when there is a continuous stream of air passing over the wood the layer of air in immediate contact with the wood will move more slowly and have a higher vapor pressure than the main stream.
This is known as the ‘boundary layer effect’. With increasing air velocity in the main stream this effect decreases and evaporation rates from the wood surface increase, particularly when the air flow is turbulent rather than laminar.
An increase in air speed can therefore be regarded as equivalent to a reduction of the humidity barrier near the wood surfaces.
Since air passing through a stack of wet wood gives up heat and takes up moisture it is bound to be cooler and more humid where it emerges than where it enters and the drying rate is therefore slower on the air outlet than on the air inlet side of the stack.
The faster the air speed and the narrower the stack, the smaller is the difference between the two sides.
For this reason fairly high air speeds are desirable in a drying kiln, particularly when the timber being dried is very wet and loses its moisture readily.
In most modern kilns the uniformity of drying is further improved by reversing the direction of air flow through the kiln load at regular intervals.
4. Movement of Moisture in the Wood
When water evaporates from the surface of a piece of wet wood the moisture content in the outer zone is lowered and moisture begins to move outwards from the wetter interior.
In practical terms this movement of moisture can be accepted as being a combination of capillary flow and moisture diffusion, a process which is resisted by the structure of the wood, particularly in dense hardwood species.
If the rate of water loss by evaporation exceeds the rate at which moisture from the wet interior can pass to the surface, the moisture gradient within the wood becomes progressively steeper.
As the outer layers dry below the fiber saturation point their tendency to start shrinking is resisted by the wetter interior so that stresses develop. If these stresses become large they can lead to a number of drying defects.
In both air and kiln drying the establishment of a moisture gradient is unavoidable and indeed desirable, for in any particular piece of wood at a given temperature the rate of movement of moisture up to the surface is proportional to the steepness of the gradient.
The skill in timber drying lies in controlling the rate of evaporation to match the rate at which moisture is reaching the surface; the aim is to maximize the moisture gradient without damaging the timber.
5. Supply of Heat
A supply of heat is required to dry timber.
In kiln drying, sensible heat is needed to raise the temperature of the wood and the water it contains to the required drying temperature, and latent heat is needed to evaporate the water.
To give an impression of the amounts of energy involved, the drying of 15 cubic meters of timber from green to 20% moisture content by electricity could require a minimum of 3000kWh.
Energy is a major element in the running costs of conventional kilns which vent warm, moist air to the outside and therefore recover none of the drying energy input.
As the relative cost of energy rises, efficient heat utilization has become a more significant factor and much attention has been given to techniques which might reduce expenditure on energy.
These range from simple upgrading of kiln insulation to the development of heat pump kilns.