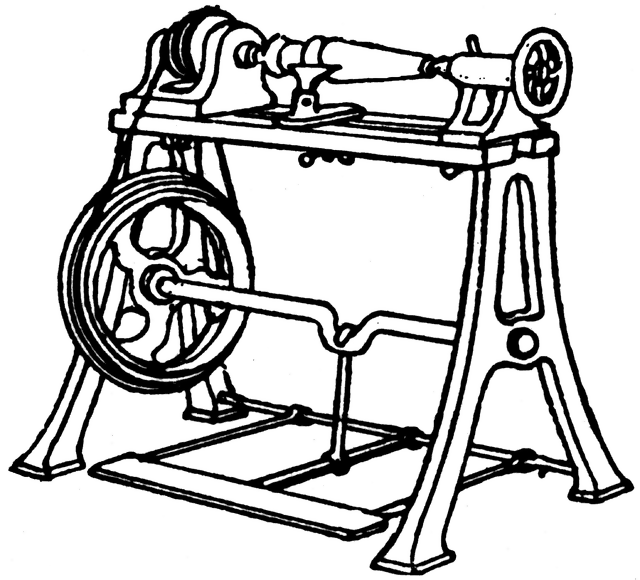
Are you looking to get into Woodturning? Then you’ve come to the right place. Follow these five steps and you’ll be well on your way.
1. Make some friends with experience.
The best advice I can give to everybody is join the local wood turning club or association, there you will be able to get some of the best information about all the perspective’s of wood turning.
Meeting people whom have the same interest as yourself, will encourage you and start you in the right direction.
Many of the members have had years of practice and each will have there own preferred method of turning, favorite lathe, and tools.
Listen closely to any advice you receive especially concerning the safety aspect.
Of course there is always the local library for books, and the internet where you can contact Wood Turners from all over the world.
Many professional wood turners have produced exceptional video’s of themselves turning everything from hollow forms to box’s and pens.
2. Get yourself some wood.
To start with go to your local timber merchant or carpenters shop and purchase all the scrap wood of at least 2″ x 2″ x 6″ and larger.
This will be used to practice on, it doesn’t matter if it hard or soft wood as the more types you initially use the better.
The reason buying wood is recommended is that the timber will be dried and of reasonable quality, which makes for better turning material.
3. Get yourself some tools.
Turning is an art form, just as painting, and music, both of which have to be practiced daily.
When you first start to turn I would advise you to purchase the following tools and limit yourself to this basic set.
For Bowl Turning:
- 1″ skew chisel.
- 1/2″ super flute gouge.
- 3/4″ or 1″ roughing gouge
- 3/8″ bowl gouge
- 1″ or 3/4″ square end scraper.( Heavy )
- Parting tool
For Spindle Turning:
- 1/2” skew chisel
- Three spindle gouges 1/4″ 3/8″ 1/2″
- 3/4″ roughing gouge
- 3/8″ beading chisel
- Parting tool
All of the above items should be made of High Speed Steel.
Sharpening Devices
Dry Grinders
This is an essential piece of shop equipment especially for the wood turner, this is probably the most affordable piece of machinery that you will buy, costing $40 to $100.
I prefer a 6″ x 1″ carborundum stone, also the grinder should be slow running.
As there is a risk of burning the tool when running at hi-speed, and if you are not very careful it is possible to remove too much steel, and end up with a misshapen tool.
However as time goes on and you become accustom to the speed of sharpening, so you will find that the lighter the touch the better the grind.
A small container of water should be available at all times to cool the tools before they become discolored and loose there hardness.
Wet stone grinder
Most wet stone grinders are slow very running approximately 70rpm. is the standard, but these stone are invariably soft and wear fast, needing frequent truing and reshaping.
The edge they produce is superior to the dry grinder, but the cost of the can be very high in comparison.
You can expect to pay anything from $140 to almost $400 for the best.
4. Get Yourself a Lathe.
There are so many lathes for sale these days, its hard to choose which one to buy.
There are many things to look out for when buying a lathe, a few of which I have listed here.
My first lathe was a cheap Chinese lathe which constantly needed repair, but it lasted long enough for me to earn enough money to buy a Myford, on which I completed some more adventurous items.
Size
Small If you have no real wish to turn large bowls or vase’s, and your real interest lays in turning pens, small boxes and items of a small delicate nature a machine with a bed of 16″ or less would suffice, with a ¾ hp or less motor.
Regular If your interests lay in larger items 12″ and larger bowls and table legs, hollow forms I would suggest a lathe of 36″+ bed length and a 1hp+ motor.
The smaller of this type of lathe can be bench mounted, however many have there own stands of steel/cast construction.
Large Some of these lathes have a huge 5hp motor and massive bearings to enable them to spin the largest of timbers.
Principally used for bowls and hollow form work, these lathes are the possessions of professional turners.
Weight and Construction
The weight of the machines affects not only the price, but also its operation.
Heavier machines have less vibration, and are more stable.
You may purchase a 500 lb lathe and think you might solve this problem, this is not so.
Weight is only an advantage when the machine is of top quality.
A good high quality fine grained cast iron casting is the start of a good lathe.
Bearings are of utmost importance not only because they have to support on object spinning at high speed, but also to help dampen vibration.
Any good lathe will have three or four heavy bearings in the headstock (business end).
All tightening handles should be cast or steel, as plastic will break eventually.
One thing which can cause you some dismay is buying your lathe and the finding out that you can not get a chuck to fit it.
This has happened to me and it can be extremely frustrating.
Check out the headstock shaft size to make sure you can get the extras you might require later on in your turning career.
Price
We would all like a high quality lathe but unless you have an unlimited bank account purchase the very best you can afford, even if you have to borrow from the bank.
A lathe is like a workshop: it’s never big enough, or has the features you require. Many lathes enable you to add on after, but at a price.
Supplier
This is where the advice of the club members really shines, if they have had a bad experience with a supplier, you can be sure that you will too.
Many Supplier’s give you thirty days to return an item which doesn’t meet your satisfaction, others offer a years warranty.
Read the small print carefully several times, if you are unsure about anything ask before placing your order.
The country of manufacture is also of importance if parts are not available in your home country.
Also, beware of things made in China as many items are of poor quality.
Some lathes are made to order, so you can expect to wait as long as six months for your new machine to arrive.
Others can be purchased anywhere, and are readily available.
Delivery
This can really be a head ache, as some manufactures will send their equipment out and you’ll take a day off from work to welcome your new lathe home, only to find out it’s going to be delivered the next day… to the curbside!
There are so many stories about deliveries, I always think you get what you pay for.
Try to insist that your delivery is tracked every step of the way, and is fully covered by insurance.
Watch out for the little extra’s for assisting you to carry the machine into the garage, there are several levels of service supplied by most freight companies, make good use of them.
If the lathe is very heavy get some friends around that day to give you a hand, the more the merrier, as many hands make light work.
Final Location
Locating the right spot to plant your newly acquired lathe can sometimes be a nightmare.
If you have a workshop with plenty of natural light this can be of a great advantage.
Most of us are forced to the basement, garage or some other room.
Wherever your locate your lathe it must be inaccessible to children, phones, and interruptions of any kind.
My family realized how dangerous it can be when a piece bark flew of a natural bowl missing my wife by inches.
It scared her and that was the best thing as she learned not to disturb Dad when he’s hiding in the workshop.
The workshop must be well lit have an adequate power supply as blackouts, and searching for fuses/breakers are annoying interruption.
Removal of dust and shavings is easier if one doesn’t have to pass through the house.
5. Start getting some practice in.
Now that you have all your equipment and some material, it’s time to start getting in some practice.
Practice between centers, turning it round using the roughing gouge, and skew chisel to form a cylinder.
Practice on a few pieces until you feel comfortable with the tools and the finish.
Don’t throw away the imperfect items, but analyze them and find your own mistake’s.
A lot can be learned by self criticism, but not by self praise.
If you are at your wit’s end and need help call on a member of the club, many give advice and lessons freely.
Search the local library or the internet for courses, as the mistakes you teach yourself are hard to correct.
We all have to start somewhere, and the best place is with the guidance of a good instructor.
Happy Turning!
I have some 4″ diam pieces of Viburnum from a tree I cut down last year. I started to turn a piece but the smell (sewage?) was nausiating. I cannot find any list of timber toxicities that list Viburnum. Can anyone throw a light on it (or some deodorant)